OBBherr
Registered

Last seeason I replaced several R1 points with R3. I failed to either cover or remove them over the winter (mea culpa.....). On preparing for this season I find that:
1. Three of the new R3 versions have rusty cover retaining screws (photo 1). I've disassembled one with some difficulty (due to collapse of corroded screw head) and the motor inside is untoched by corrosion.
2. Two of the new R3 versions (from same batch) are still bright and unrusted (photo 2 and 3)
3. My old R1 point screws are still bright after a number of seasons outside
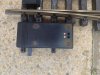
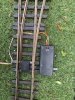
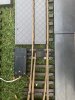
So if you will forgive a multipart question:
a. Has anyone else experienced problems with LGB point screws corroding?
b. Can you suggest a source for replacements, both for the cover screws, and more importantl the grub screws on the electrical terminals (also corroded)
c. Can you recommend something waterproof to drop onto the screw heads to stop a recurrence but which will peel off if needed? I'm thinking someting like a blob of Copydex or similar?
Thanks in advance for any insights and advice.
1. Three of the new R3 versions have rusty cover retaining screws (photo 1). I've disassembled one with some difficulty (due to collapse of corroded screw head) and the motor inside is untoched by corrosion.
2. Two of the new R3 versions (from same batch) are still bright and unrusted (photo 2 and 3)
3. My old R1 point screws are still bright after a number of seasons outside
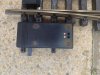
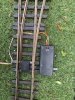
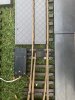
So if you will forgive a multipart question:
a. Has anyone else experienced problems with LGB point screws corroding?
b. Can you suggest a source for replacements, both for the cover screws, and more importantl the grub screws on the electrical terminals (also corroded)
c. Can you recommend something waterproof to drop onto the screw heads to stop a recurrence but which will peel off if needed? I'm thinking someting like a blob of Copydex or similar?
Thanks in advance for any insights and advice.