I now have 12 window frames for the ex-Jackson, all in primer awaiting a dry day (where I'm also home in the daylight) for a coat of paint. The brake van now has some handrails and is ready to be painted.
A few updates back I mentioned I had picked up a couple of Piko ore hoppers for a conversion. Back in 1899 the Furness Railway ordered a pair of 45 ton bogie hoppers from the Pressed Steel Car Company in the USA. 10 more were ordered from a domestic supplier and some survived until the 1950's as internal user wagons in steel mills. My plan was to back date the Piko offerings to something similar.
Photo taken from here
How did a small narrow gauge line, in an unimportant part of the Midlands end up with such luxurious wagons? Well, the primary reason for the existence of the N&L.L.R is to move bulk quarry products. Aggregate, sand, clay and bulk rock were pulled out of ground in no less than 12 pits served along the line's length. Excluding the largest few which had their own branch line running directly into the good yard at Narborough, the quarries' products had always been transported in small 4 wheel tubs along the main line in their own trains. When the LMS inherited the line, to say they were offended by the practice of running long trains of unbraked, unsprung and poorly maintained 'minecarts' along the same line as the principal passenger and regular goods services, was putting it lightly. Something would have to be done...
The Piko wagons are very simple, made of two mouldings; the body and the baseplate. The first step of the conversion was to remove all of the moulded handrails from the wagon and sand back the joints.
The try and more closely match the basic silhouette of the prototype, the open half of the side plating was filled in with 2mm Plasticard. A triangle was added to the bottom of the chassis rail and reinforced from the back. Another rectangle of card was added to create the space where the large central strap attaches the body to the frame.
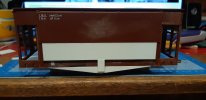