I have the holy trinity of SLA, FDM and laser cutter. All do very different jobs.
Most consumer SLA printers use UV light shone through an LCD screen. This creates the layer mask and the exposed resin then hardens to that shape. Great for making figures, small detail parts and anything where visible lines might be a problem to hide. There's a couple of common sizes of printers and something like an Elegoo Saturn will print quite large items, but the running costs will be high. Resin is currently around £30 per KG, and some wastage will occur. As others have said, its smelly, messy and really needs a dedicated workshop with artificial lighting to work well. Sunlight will set the resin instantly, but typical UV blocking glass will prevent this. You also need copious amounts of ipa to clean the prints and printer, along with either an electrical agitator or plenty of manual swirling and brushing of parts to clean up the excess resin. Gloves always required!
I have a Creality Ender 3 Pro and I'm very happy with it. Previously I had a dual extruder CTC 3D which I fully enclosed and got quite acceptable results with as well. A good surface finish is not just about resolution, but also accuracy and repeatability. A printer needs to deposit the next layer precisely upon the last and at exactly the right height to reduce the visible lines, ringing and surface imperfections. Painting with a high fill primer will improve things further, but a really good finish needs some elbow grease with the sander. While SLA is effectively 1 speed - the layer is exposed for the same amount of time irrespective of how large the or complex the layer is, FDM printers can be run at a variety of speeds. Increasing the layer height and print speed degrades quality, but for drafting an initial prototype, it's very useful.
While you are limited to a handful of different resins with a small range of colours and physical properties with SLA, FDM printers have a wider range of materials and a huge colour gamut to choose from. PLA is the most popular, being easy to print, ABS is generally a slightly stronger material but needs a heated bed and ideally an enclosed build chamber to prevent warping while printing, PETG is more flexible once printed and is excellent for functional parts like couplings while more exotic materials like Ninjaflex and Chopped Carbon may require modifications to the printer, but increase the range of components that can be made.
Laser cutting of thin ply using an LED laser is relatively easy to do and the design process is simpler as you are only working in 2D. A well ventilated space is a must, and I've added an air assist nozzle to mine, which increases cutting depth and finished part quality by reducing charring. I can cut up to 3mm ply, which is very useful for G Scale rolling stock and buildings etc. plus thick card and some perspex materials. Don't take any risks with open frame laser cutters. Momentary exposure to the direct or reflected beam could blind you permanently. Buy some safety glasses or build an enclosure.
I user Microsoft 3d Builder, Siemens Solid Cad 2D, Tinkercad and Light Burn for the majority of design tasks. I also have Inkscape for tracing images to vectors and various other tools for file conversion and manipulation. My only paid software is Simplyfy 3D for FDM slicing and Lightburn for basic laser 2d shapes and to control the cutter.
I've posted a few makes and files on this forum, so please just search my user name. All stock in the photo below with the exception of the MSS loco and 2 trams is either 3d printed or laser cut by me. The Wisbech and Upwell coach was drawn by me from images supplied by
dunnyrail
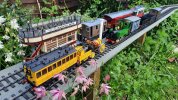