Hi Everyone,
I noodle around in my basement with different setups until I've annoyed the family up to the point of causing major strife and then pick it all up. As such there is nothing in my setup that's permanent and it also changes the cost/benefit calculus of spending big bucks on DCC equipment when I have perfectly good analog stuff to play with. I've been having fun with automating my setup and trying to replicate some of the automated layouts from the old World of LGB book like: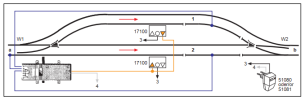
that alternates between the train on track 1 and 2, letting one run the circuit while the other waits in the station. I've also successfully combined it with an automated reversing loop at one point. It's been fun to figure out how to wire everything and plan a layout that incorporates the more interesting aspects of controlling trains automatically.
On the aesthetic side, however, it is pretty jarring when power is simply cut to one train as it enters the de-energized track in front of a signal. Same goes for start up on the other train that has now been energized. You get the wagons all crashing into each other or watch the loco starting up with the proverbial pedal to the metal. As such I was trying to think of ways to introduce more controlled slowdowns and startups.
My thought was to wire a capacitor up to the portion of the track that is de-energized by the signals. In my rudimentary understanding, the capacitor would then discharge power, slowly dropping power until the train stops (assuming the train won't blow through the signal) and when the track is re-energized, the capacitor will first draw down some of the power before and then slowly start passing power through too the energized track. (By the way, I'm saying power here because I don't know if it's voltage or current or both that are being affected.) Given my non-permanent setup, I'm looking for something flexible that can be applied in a number of designs where a train is stopped by the automatic signals. To my understanding, things like the sophisticated train controllers, Bridgewerks, Jumbo and others won't achieve this with multiple trains all on the same layout, but I'm happy to be proven incorrect.
An alternative I had considered is to use a bunch of 10153s with diodes to drop voltage over each segment prior to the dead section. This would at least make the slow down more controlled, but it wouldn't change the start up part.
Would appreciate any advice or thoughts you have. Also, is there any good way to calculate/guesstimate the size of capacitor to get? Currently was thinking 40000 uF, 25 VDC capacitors as per the automated block design from James Ingraham at automatedcontrols.org, but it would be good understand how far a train will go given a particular capacitor size.
Finally, is there anything that might damage equipment or be hazardous based on what I've described?
Thanks!
I noodle around in my basement with different setups until I've annoyed the family up to the point of causing major strife and then pick it all up. As such there is nothing in my setup that's permanent and it also changes the cost/benefit calculus of spending big bucks on DCC equipment when I have perfectly good analog stuff to play with. I've been having fun with automating my setup and trying to replicate some of the automated layouts from the old World of LGB book like:
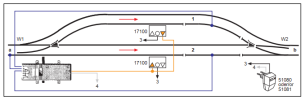
that alternates between the train on track 1 and 2, letting one run the circuit while the other waits in the station. I've also successfully combined it with an automated reversing loop at one point. It's been fun to figure out how to wire everything and plan a layout that incorporates the more interesting aspects of controlling trains automatically.
On the aesthetic side, however, it is pretty jarring when power is simply cut to one train as it enters the de-energized track in front of a signal. Same goes for start up on the other train that has now been energized. You get the wagons all crashing into each other or watch the loco starting up with the proverbial pedal to the metal. As such I was trying to think of ways to introduce more controlled slowdowns and startups.
My thought was to wire a capacitor up to the portion of the track that is de-energized by the signals. In my rudimentary understanding, the capacitor would then discharge power, slowly dropping power until the train stops (assuming the train won't blow through the signal) and when the track is re-energized, the capacitor will first draw down some of the power before and then slowly start passing power through too the energized track. (By the way, I'm saying power here because I don't know if it's voltage or current or both that are being affected.) Given my non-permanent setup, I'm looking for something flexible that can be applied in a number of designs where a train is stopped by the automatic signals. To my understanding, things like the sophisticated train controllers, Bridgewerks, Jumbo and others won't achieve this with multiple trains all on the same layout, but I'm happy to be proven incorrect.
An alternative I had considered is to use a bunch of 10153s with diodes to drop voltage over each segment prior to the dead section. This would at least make the slow down more controlled, but it wouldn't change the start up part.
Would appreciate any advice or thoughts you have. Also, is there any good way to calculate/guesstimate the size of capacitor to get? Currently was thinking 40000 uF, 25 VDC capacitors as per the automated block design from James Ingraham at automatedcontrols.org, but it would be good understand how far a train will go given a particular capacitor size.
Finally, is there anything that might damage equipment or be hazardous based on what I've described?
Thanks!