AlanL
Registered

I have a Bachmann Gandy Dancer Handcart which had been stored away in the attic for many years after it's drive belt had broken. I believe that it is the earlier version that has the drive belt, later versions I believe have a more reliable worm drive. I had forgotten about it but a thread last October reminded me that I had one languishing in the attic.
I had a look at it and confirmed that the drive belt was broken. I measured the remains of the broken belt and guessed that it was 2 mm section by 16 mm diameter. To me it looked like a nitrile 'O' ring and I ordered a pair to try, they are relatively cheap so it was worth a try.
To fit the new drive belt, the motor has to be dismantled because the belt fits inside the motor casing. this is not a difficult job however the springs for the brushes are extremely small and lively! I had to do a forensic search on my workshop floor to recover the spring. You have been warned, I didn't listen to my advice and lost a spring a second time when aligning the securing clip for the spring. Another forensic search was needed!
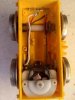
I finally managed to fit the belt and re-assemble the hand cart.
Now to test it. The hand cart is analogue and I don't have an analogue controller (I used to but had a too hasty clear out). But I do have a 24 volt power supply and a length of track and with 24 volts connected, the hand cart zoomed away.
So that was encouraging and the estimated guess at the 'O' ring size was okay. However an analogue handcart was no use to me as I only have a DCC railway.
Could I fit a decoder to it?
At first look, the only place was on the top platform of the trailer but looking at small decoders there was a possibility that I could fit one in the space on the trailer between the upper platform and the chassis platform.
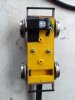
The decoder that I used was an LGB 55022 and was just small enough to fit the space. This article is not about the decoder fitting so I will be brief and say that it involved taking 4 wires between the trailer and the main handcart.
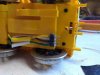
I happened to have in my 'bits' some 'single in line sockets' and these were used as a plug connection between the two units.
So with the decoder fitted and wired it was time to test.
To be honest, it didn't work on my test track but by using an LED into the track connections to the decoder, the problem was seen to be the track power pickup.
Having got this far, do I give up or rise to the challenge?
I decided to rise to the challenge and studied the units to find a way to improve the pickup.
The main unit contains the motor and gearing and looked impossible to fit any pickups. The trailer had more space and after some thought I fitted some long brass strips screwed underneath the chassis platform with their ends just contacting the axles.
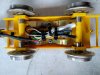
This was only a slight improvement and the contact pressure of the strips onto the axles was critical, too much contact stopped the axles rotating.
After this I went to my local model shop to purchase some thinner brass sheet. while there I explained what I was doing and they suggested some Phosphor bronze strips that they stock specifically for use as contact strips.
They come in a pack of 10 and I soldered some short lengths on top of the original brass strips that I bent away from the axle to accommodate the phosphor bronze strips. The idea was that they are more flexible and lighter on the axle. Another test showed that the track power was still intermittent at the decoder so another think was required. I had previously dismissed fitting any pickups to the main unit but these strips were only 1.5 mm wide and with some ingenuity I found that I could solder four strips edge-on to the main unit metal chassis rails so that they made contact with each pair of axles. Unfortunately I don't have any pictures of these, i couldn't get a decent photo due to them being so small and partly hidden behind the axles.
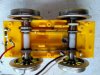
Testing on the test track had the best result so far and decided that it was time to test it on the club layout.
Running was faultless until I ran in reverse and thereafter it failed to run. Inspection afterwards showed a build-up of dirt between the contacts and the axles.
After another thinking session I decided to try pickups directly onto the track. The trailer was really easy to do without any modification. It involved bending a piece of brass 25 mm wide into an 'L' shape and soldering a length of phosphor
bronze to contact the track, easier to see in the photo than describe.
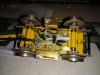
The brass simply slotted into the space between the trailer metal chassis pieces and the edge of the lower platform. The brass was bent slightly to make an interference fit.
This arrangement worked well until I reversed over a set of points. How did I miss this, the open ended pickups snagged in the gap at the frog, (I've no points on my test track).
After another thinking session I decided that I could fit full length pickups by using a sheet of phosphor bronze. (Phosphor bronze in sheet form in varying thicknesses is available from some electronics suppliers).
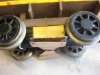
These pickups were shaped to give them more flexibility by reducing their width to 10 mm toward their innermost point.
Although this was an ugly addition it was an improvement and my thoughts now turned to the main unit.
I wondered if it was possible to add any track pickups to the main unit. It is crammed inside with the motor and drive train, the underside is not level and it does not have any thickness to screw anything to it. Studying the underside of the main unit I noticed that although there were different levels there was a common level on each side that I could use to make a larger mounting for track pickups. I had some 4 mm acrylic that I shaped to fit each side and then glued in place. Before gluing I had considered the shape of the pickups, their fixing positions and drilled them for the pickups. I could only use short screws, 5 mm in length so I did use some M3 machine thread screws shortened to 5 mm and tapped the holes in the acrylic accordingly.
The photo shows the new track pickups and the black tape keeping the connector to the trailer in place. It also shows the lead weight that I added to improve the traction of the handcart. One disadvantage of the track pickups is the drag and they try to lift the wheels off the track. I also added lead inside the main unit. Even with this the handcart would sometimes get wheel slip so I added another two rolls of lead on the top platform.

Now it runs faultlessly on the club layout. It even runs at speed setting 1 without any hesitation. But in the garden the track needs to be mega clean. The new pickups are too light to push through any dirt or dust on the track as the big locos would.
The new pickups stick out in the photo but when it is running your eyes are drawn to the two gandy dancers working hard to keep it moving.
It's been an interesting project that I thought that I could share.
Would I do it again?
If I did I would go straight to the track pickups. they are more reliable than trying to use the wheels and axles to conduct track power, maybe something to do with the metal or lack of plating?
Fitting a battery would be a lot easier.
Alan
I had a look at it and confirmed that the drive belt was broken. I measured the remains of the broken belt and guessed that it was 2 mm section by 16 mm diameter. To me it looked like a nitrile 'O' ring and I ordered a pair to try, they are relatively cheap so it was worth a try.
To fit the new drive belt, the motor has to be dismantled because the belt fits inside the motor casing. this is not a difficult job however the springs for the brushes are extremely small and lively! I had to do a forensic search on my workshop floor to recover the spring. You have been warned, I didn't listen to my advice and lost a spring a second time when aligning the securing clip for the spring. Another forensic search was needed!
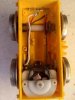
I finally managed to fit the belt and re-assemble the hand cart.
Now to test it. The hand cart is analogue and I don't have an analogue controller (I used to but had a too hasty clear out). But I do have a 24 volt power supply and a length of track and with 24 volts connected, the hand cart zoomed away.
So that was encouraging and the estimated guess at the 'O' ring size was okay. However an analogue handcart was no use to me as I only have a DCC railway.
Could I fit a decoder to it?
At first look, the only place was on the top platform of the trailer but looking at small decoders there was a possibility that I could fit one in the space on the trailer between the upper platform and the chassis platform.
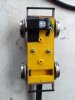
The decoder that I used was an LGB 55022 and was just small enough to fit the space. This article is not about the decoder fitting so I will be brief and say that it involved taking 4 wires between the trailer and the main handcart.
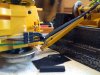
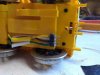
I happened to have in my 'bits' some 'single in line sockets' and these were used as a plug connection between the two units.
So with the decoder fitted and wired it was time to test.
To be honest, it didn't work on my test track but by using an LED into the track connections to the decoder, the problem was seen to be the track power pickup.
Having got this far, do I give up or rise to the challenge?
I decided to rise to the challenge and studied the units to find a way to improve the pickup.
The main unit contains the motor and gearing and looked impossible to fit any pickups. The trailer had more space and after some thought I fitted some long brass strips screwed underneath the chassis platform with their ends just contacting the axles.
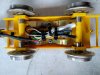
This was only a slight improvement and the contact pressure of the strips onto the axles was critical, too much contact stopped the axles rotating.
After this I went to my local model shop to purchase some thinner brass sheet. while there I explained what I was doing and they suggested some Phosphor bronze strips that they stock specifically for use as contact strips.
They come in a pack of 10 and I soldered some short lengths on top of the original brass strips that I bent away from the axle to accommodate the phosphor bronze strips. The idea was that they are more flexible and lighter on the axle. Another test showed that the track power was still intermittent at the decoder so another think was required. I had previously dismissed fitting any pickups to the main unit but these strips were only 1.5 mm wide and with some ingenuity I found that I could solder four strips edge-on to the main unit metal chassis rails so that they made contact with each pair of axles. Unfortunately I don't have any pictures of these, i couldn't get a decent photo due to them being so small and partly hidden behind the axles.
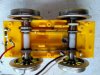
Testing on the test track had the best result so far and decided that it was time to test it on the club layout.
Running was faultless until I ran in reverse and thereafter it failed to run. Inspection afterwards showed a build-up of dirt between the contacts and the axles.
After another thinking session I decided to try pickups directly onto the track. The trailer was really easy to do without any modification. It involved bending a piece of brass 25 mm wide into an 'L' shape and soldering a length of phosphor
bronze to contact the track, easier to see in the photo than describe.
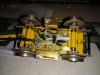
The brass simply slotted into the space between the trailer metal chassis pieces and the edge of the lower platform. The brass was bent slightly to make an interference fit.
This arrangement worked well until I reversed over a set of points. How did I miss this, the open ended pickups snagged in the gap at the frog, (I've no points on my test track).
After another thinking session I decided that I could fit full length pickups by using a sheet of phosphor bronze. (Phosphor bronze in sheet form in varying thicknesses is available from some electronics suppliers).
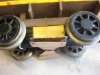
These pickups were shaped to give them more flexibility by reducing their width to 10 mm toward their innermost point.
Although this was an ugly addition it was an improvement and my thoughts now turned to the main unit.
I wondered if it was possible to add any track pickups to the main unit. It is crammed inside with the motor and drive train, the underside is not level and it does not have any thickness to screw anything to it. Studying the underside of the main unit I noticed that although there were different levels there was a common level on each side that I could use to make a larger mounting for track pickups. I had some 4 mm acrylic that I shaped to fit each side and then glued in place. Before gluing I had considered the shape of the pickups, their fixing positions and drilled them for the pickups. I could only use short screws, 5 mm in length so I did use some M3 machine thread screws shortened to 5 mm and tapped the holes in the acrylic accordingly.
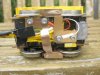
The photo shows the new track pickups and the black tape keeping the connector to the trailer in place. It also shows the lead weight that I added to improve the traction of the handcart. One disadvantage of the track pickups is the drag and they try to lift the wheels off the track. I also added lead inside the main unit. Even with this the handcart would sometimes get wheel slip so I added another two rolls of lead on the top platform.

Now it runs faultlessly on the club layout. It even runs at speed setting 1 without any hesitation. But in the garden the track needs to be mega clean. The new pickups are too light to push through any dirt or dust on the track as the big locos would.
The new pickups stick out in the photo but when it is running your eyes are drawn to the two gandy dancers working hard to keep it moving.
It's been an interesting project that I thought that I could share.
Would I do it again?
If I did I would go straight to the track pickups. they are more reliable than trying to use the wheels and axles to conduct track power, maybe something to do with the metal or lack of plating?
Fitting a battery would be a lot easier.
Alan
Last edited: