JohnSol
Registered

A couple solder joints on my Accucraft C&S 60 failed. I tried fixing them with a 250 watt soldering gun. The results were disgusting. Soldering on these models is tricky business.
Recently, I've been experimenting with Resistance Soldering. I've tried different power units, probes, tweezers and electrode materials. At this point I'm on the low end of the learning curve. My last test involved a modified probe. Originally a wire stripper with two leads to the power unit, I removed the internals and machined a brass holder for a five millimeter carbon electrode (see attachment.)
Testing with different shaped carbons at wattages ranging from 130 to 250 on small .020" thick brass squares and tubes yielded results that ranged from damaging the brass to good joints with the solder melting almost instantly.
Obviously, I'm nowhere near the needed proficiency to work on brass models. Outside of continuous experimentation, is there any guidance for soldering and repairing brass models?
Recently, I've been experimenting with Resistance Soldering. I've tried different power units, probes, tweezers and electrode materials. At this point I'm on the low end of the learning curve. My last test involved a modified probe. Originally a wire stripper with two leads to the power unit, I removed the internals and machined a brass holder for a five millimeter carbon electrode (see attachment.)
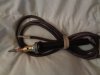
Obviously, I'm nowhere near the needed proficiency to work on brass models. Outside of continuous experimentation, is there any guidance for soldering and repairing brass models?