gregh
electronics, computers and scratchbuilding

Lilyvale is the only 'town' on my railway and I decided I wanted a 'substantial' building for the post office – approx the same size as the pub which it will be adjacent to. I like the Post and Telegraph Office at the real town of Sandstone WA, but wanted a clock tower. So this montage shows what I envisaged. (apologies for the quality of this montage)
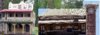
Hebel (Thermalite in UK ?) lightweight concrete blocks seemed the ideal material as I have previously made station buildings and goods sheds from it. It's easy to carve and can stay outside in all weathers.
For more info on working with Hebel, see my webpages here:
http://www.members.optusnet.com.au/satr/hebel.htm
I drew some plans using Word Draw and decided on a scale of 1:30 so the buildings are a little smaller than my usual 1:25 scale.
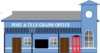
By playing around with dimensions, I was able to use just a single 200x200x600mm (8”x8”x24”) block. Using a bush saw, I cut 150mm off the end – so the main body of the building will be 200x450.
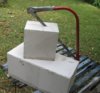
From the 150x200x200 piece, I cut two pieces 75x75x200 for the clock tower and two pieces 75x100x200 to form the 'add-on' rooms at the back. So the final 'footprint' is 275 x 450mm.
Then using a hand saw, I carefully cut the 'slopes' of the roof and used a rasp to smooth off the cuts.
(the roof will be covered in corrugated aluminium)
Here's the bits 'mocked-up'. (the tower will not be that high.)
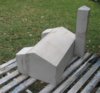
Then I started making windows and doors from styrene. The yellow ones are from a peg basket from a $2 shop. These fit into cutouts in the hebel.
I used 'frosted' plastic for the windows, from milk bottles, so you can't see in.
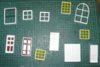
The cutouts are made using whatever is suitable – hacksaw blade, chisel, knife, drills and spade bits. The window cutouts are around 40mm deep and will be painted black – there is NO interior detail.
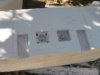
Once all the cutouts were done, I could start scribing the stone courses using a hacksaw blade. This is a long, dusty job, best tackled in small stages.
This is the back, and the circular holes are 'keys' for the glue that will hold the add-on 'extension' rooms.
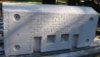
The 'add-on' 'rooms' are glued with Fullers Ultra Clear silicone, and nailed with 4” nails.
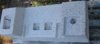
Then I coloured the sandstone with cement oxides mixed with water and brushed on.
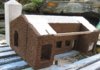
wait for the next exciting installment...
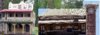
Hebel (Thermalite in UK ?) lightweight concrete blocks seemed the ideal material as I have previously made station buildings and goods sheds from it. It's easy to carve and can stay outside in all weathers.
For more info on working with Hebel, see my webpages here:
http://www.members.optusnet.com.au/satr/hebel.htm
I drew some plans using Word Draw and decided on a scale of 1:30 so the buildings are a little smaller than my usual 1:25 scale.
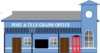
By playing around with dimensions, I was able to use just a single 200x200x600mm (8”x8”x24”) block. Using a bush saw, I cut 150mm off the end – so the main body of the building will be 200x450.
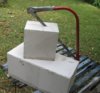
From the 150x200x200 piece, I cut two pieces 75x75x200 for the clock tower and two pieces 75x100x200 to form the 'add-on' rooms at the back. So the final 'footprint' is 275 x 450mm.
Then using a hand saw, I carefully cut the 'slopes' of the roof and used a rasp to smooth off the cuts.
(the roof will be covered in corrugated aluminium)
Here's the bits 'mocked-up'. (the tower will not be that high.)
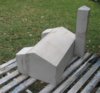
Then I started making windows and doors from styrene. The yellow ones are from a peg basket from a $2 shop. These fit into cutouts in the hebel.
I used 'frosted' plastic for the windows, from milk bottles, so you can't see in.
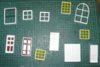
The cutouts are made using whatever is suitable – hacksaw blade, chisel, knife, drills and spade bits. The window cutouts are around 40mm deep and will be painted black – there is NO interior detail.
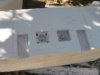
Once all the cutouts were done, I could start scribing the stone courses using a hacksaw blade. This is a long, dusty job, best tackled in small stages.
This is the back, and the circular holes are 'keys' for the glue that will hold the add-on 'extension' rooms.
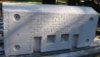
The 'add-on' 'rooms' are glued with Fullers Ultra Clear silicone, and nailed with 4” nails.
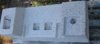
Then I coloured the sandstone with cement oxides mixed with water and brushed on.
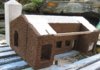
wait for the next exciting installment...