tramcar trev
all manner of mechanical apparatus...
I have managed to rip up my ballast which was laid with dry cement mixed in and the dampened with a water mist. It set OK and held together for a while but it soon cracked and split up... Came up rather easier than I thought too in big lumps. One of the section bonds was broken in the exercise so that was resoldered. This also solved another problem; I had a voltage drop on the balloon
loop where the ballast is laid.
Minimum jack hammering required!!
I relayed it; and this time used a mixture of 50/50 water and exterior grade Aquadhere with a small amount of dishwasher rinse aid to act as a wetting agent.... Of course I made a test coupon first on a bit of 3 ply allowed it to dry and then twisted it every way and it stayed in place, more flexible than being held by cement. This is a departure for me testing things out before I jump in to the deep end, I may be learning. The other thing I noticed is that the earlier ballast (aka crusher dust) had particles in it that are magnetic and this played havoc with the magnets under the trams for the signalling system. The ballast that I’m using now has no magnetic particles in it yet still looks like your everyday crusher dust; a different source or the magnetic particles were bits of the crusher….
I used a very technical piece of apparatus to place the ballast. I got it for Xmas; it’s called a disposable teaspoon but I found that the shape of it allowed me to ensure that no ballast encroached on the flange ways especially around the 2 sets of points. Then apply the adhesive mixture with a trigger bottle until it runs off. When it dries it can’t be seen. Next task is to get out the pseudo Dremel and an abrasive mop and clean up the track to allow conductivity. A far more realistic and “flexible” solution to the problem of the moving ballast.
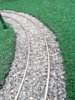
Minimum jack hammering required!!
I relayed it; and this time used a mixture of 50/50 water and exterior grade Aquadhere with a small amount of dishwasher rinse aid to act as a wetting agent.... Of course I made a test coupon first on a bit of 3 ply allowed it to dry and then twisted it every way and it stayed in place, more flexible than being held by cement. This is a departure for me testing things out before I jump in to the deep end, I may be learning. The other thing I noticed is that the earlier ballast (aka crusher dust) had particles in it that are magnetic and this played havoc with the magnets under the trams for the signalling system. The ballast that I’m using now has no magnetic particles in it yet still looks like your everyday crusher dust; a different source or the magnetic particles were bits of the crusher….
I used a very technical piece of apparatus to place the ballast. I got it for Xmas; it’s called a disposable teaspoon but I found that the shape of it allowed me to ensure that no ballast encroached on the flange ways especially around the 2 sets of points. Then apply the adhesive mixture with a trigger bottle until it runs off. When it dries it can’t be seen. Next task is to get out the pseudo Dremel and an abrasive mop and clean up the track to allow conductivity. A far more realistic and “flexible” solution to the problem of the moving ballast.