supagav
USA standard gauge in the late 1960's, in 1:29th.
Hi folks,
I just wanted to share a few thoughts I`ve been having about how to try and make my own detail parts to try in an attempt to improve the look of our 1:29 US diesels. The problem I have always had is that there just aren`t as many parts for the kitbasher as there are in the smaller scales like HO, so I`ve always had to fabricate them. With this new 3D printing craze I thought I would try and see if I can mock up some simple detail parts like headlights etc to help me achieve a more detailed finish.
Here is a special SP style oscillating headlight called a Gyralight, which I`m trying to make in 1:29. Many thanks to James Hilton (and his blog!) for the 3D printing inspiration. I`m still not really there yet but I thought I would share my progress so far:
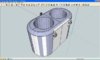
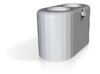
I just wanted to share a few thoughts I`ve been having about how to try and make my own detail parts to try in an attempt to improve the look of our 1:29 US diesels. The problem I have always had is that there just aren`t as many parts for the kitbasher as there are in the smaller scales like HO, so I`ve always had to fabricate them. With this new 3D printing craze I thought I would try and see if I can mock up some simple detail parts like headlights etc to help me achieve a more detailed finish.
Here is a special SP style oscillating headlight called a Gyralight, which I`m trying to make in 1:29. Many thanks to James Hilton (and his blog!) for the 3D printing inspiration. I`m still not really there yet but I thought I would share my progress so far:
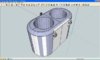
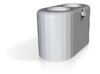