3 minutes of fame
3d printing, electronics and trams

From my fevered mind comes another little design...
Walking around the Garden Railway Show, I chatted to a trader about some of his laser cut coaches and the length of drawbars needed to get them around tighter curves.
It set me thinking that if it works at 00, it will probably work in G!
This is my first prototype, ready to fit to my W&U coach:
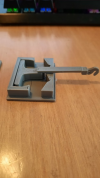
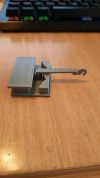
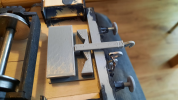
Walking around the Garden Railway Show, I chatted to a trader about some of his laser cut coaches and the length of drawbars needed to get them around tighter curves.
It set me thinking that if it works at 00, it will probably work in G!
This is my first prototype, ready to fit to my W&U coach:
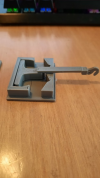
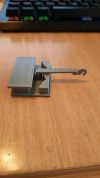
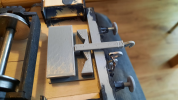